DESCRIPTION
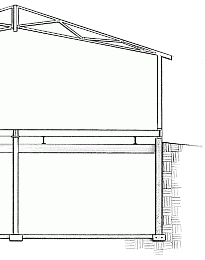
A basement is both an engineered structural support system for a manufactured home and a substantial addition to the livable space of the home. This makes the basement unique among the classes of foundations described in this guide.
After our engineers are finished, the basement becomes an integral part of the mobile home design (including site-built homes), particularly in the northern half of the country, from the Intermountain West to the Northeast. Their popularity in this region stems from the basement’s ability to give a home excellent support, even in deep frost locations, and to generate relatively inexpensive living space. This living area is particularly important to families whose outdoor activities are curtailed in the winter.
The popularity of basements in colder climates is readily apparent from the census data. Basements account for upward of 4 out of every 5 site-built home foundations in the 33 states that comprise Zone 3 of the HUD thermal standards . In the Northeast and north central states, the preference for basements climbs to 9 of every 10 homes.
Basements are well suited for sloping lots, especially lots that slope down to the back of the home. This allows our engineers to design a “walk-out” basement, featuring doors to a rear yard. Indeed, many developers create special grades to accommodate a walkout basement. If the development site is relatively level, the grading plan will call for substantially elevated pads upon which to perch the homes.
Basements are natural for “low profile” installations. Basements are typically designed by our engineers to support the full perimeter wall of the home. Typically, supports for the interior of the home are provided at the marriage line. Posts are designed by our engineers to carry the loads transferred by the floor joists and cross beams that support the chassis. Basements can be built partially or entirely above ground, creating in essence a two-story, or a split- level manufactured home. This application suggests even more varieties for home placements. Upslope lots can be developed with basements that incorporate a garage that is directly accessible from the street.
Ready to Order?If you are ready to order foundation plans, you may place your order by clicking here. |
CONSTRUCTION
Basements demand extreme care in their construction. The outside wall cannot be longer or wider than the floor of the manufactured home. If such a construction error is made, the remedy can be very expensive, or can result in a very awkward correction. The basement walls should never protrude horizontally beyond the edge of the perimeter floor joists.
Obviously, the excavation of a large quantity of soil presents a disposal problem. A certain amount of earth can be used to backfill against the basement wall to create drainage slope away from the house. But the exporting of soil becomes a budget item not usually encountered when using slabs or crawl space foundations.
Balancing the soil helps to minimize this by excavating less of the basement than would normally be anticipated. With this plan, the basement walls extend 3 or 4 ft above the natural site grade. Earth removed from the excavation is used as backfill to create a substantial grade away from the house and bring the grade to within 8-10 in. from the bottom of the floor.
Because of the size of the structure, basements require far more material (typically concrete and/or concrete blocks, if specified) than other foundations. Up to 90 cu yds or more can be for a basement for a larger two-section mobile home.
Depending on the type of basement and the method used to install home sections, the basement may or may not be fully completed before the home arrives. Homes that are to be rolled onto cross-beam girders need to have the top 6-8 in. of wall (or the top course of concrete blocks) left out, to permit the home to be rolled across the basement walls and into final position.
A well thought-out plan for securing the home to the foundation by our engineers prevents trouble later when installing the home. Since bolts can interfere with the floor joists, foundation straps may be preferable. Cutting off bolts or coring out the sill to allow for the bolt’s washer and hex nut is not recommended.
Most basements incorporate usable space and are accessed through stairwells from the upper (main) level. Walk-out basements have standard exit doors to the outside yard. In any case, a code-complying access must be incorporated into the structure’s design.
VENTILATION
A basement is usually intended to become part of the habitable space of a home and direct ventilation to the outside is not recommended. Therefore, only ventilation that can be controlled by the homeowner is used. Doors, if it is a walkout basement, and operable windows, if they are part of the design, allow natural ventilation.
Basements are often conditioned (heated and cooled), with ducted supply and return assuring adequate air changes. When the basement is part of the conditioned space, the equipment size will need to be adjusted accordingly. In such cases, the home manufacturer must be consulted for requirements covering adequate air flow, ducting, protection against heat loss, etc. A basement that will be heated by the manufactured home’s system adds greatly to the burden of the mechanical plant, and must be accounted for by the manufacturer when sizing the heating system, ducts system, and electrical system.
INSTALLATION
It is more challenging to install a manufactured home on a basement than on slab or crawl space foundations. Inevitably, the home’s sections will be maneuvered over substantial vertical heights. Many contractors who set up homes on slabs or crawl spaces are not well equipped to handle a basement. The two primary methods of installing homes on basements are the crane and the roller systems, as described below:
Crane set: Perhaps the more common of the two processes, a crane picks up and places each home section directly on the basement walls (and cross girders, if used). This permits the basement to be more fully complete before the home arrives. Provisions must be made, however, to withdraw the crane’s straps before they are trapped between the basement and the home.
A basement may also pose structural issues for the manufacturer. For example, manufactured homes in most cases are required to have a number of shearwalls that carry the loads from the wall and roof diaphragms to the foundation. These shearwalls are supported by multiple joists under each wall. Since this is a unique feature of these homes, special provisions must be made for connecting/anchoring of the multiple shearwall joists and shearwall end columns to the foundation system to ensure adequate transfer of the loads.
For a crane installation to go quickly, the setup crew and the crane operator must be experienced with this process, an appropriate strap spreader device must be used, the homes must be at the site and in position for pickup, and the crane must be able to set up fairly near the basement.
Strap (or cable) withdrawal can be accomplished by measuring and cutting portions of the sill (make sure that the foundation approvals permit this), then replacing them after the straps are pulled out. A good way to avoid trapping the straps between the sections of the home is to set the second module onto jack posts at the center line that are set at a slightly high position. The home will come down and rest in a canted posture that allows removal of the straps. The jacks can then lower the home into a level position.
The cost of using a crane varies by location. Rates are highly variable; some crane operators charge high minimums, others charge steep rates for travel time, so it is wise to shop around. In normal conditions, a two-section home can be set and made weather-tight in 4 hours.
Roller system: Popular for all types of manufactured home installations, the use of rollers is an effective way of moving homes forward, sideways, and up or down mild slopes. Rollers are best suited to place a home over an enclosed foundation system, especially a basement.
Ready to Order? If you are ready to order foundation plans, you may place your order by clicking here.
Contractors can set up the temporary columns, rails, channels, and roller devices rapidly. Special column supports are used for basement sets. Typically 2 or 3 such rails are used. The home is simply pushed sideways over the basement walls and rolled into final position. Using hydraulic jacks, the home is then lowered onto the sills and cross beams, if used. In either case, the axles, tires, and hitches are removed before the home is lifted onto or rolled over the basement.
Basement showing backfill to create drainage slope.
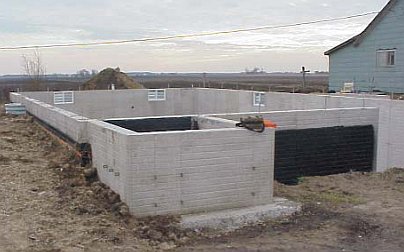
INTERIOR SUPPORTS
The supporting structure of a basement depends on whether the home has a standard or integrated floor system.
Standard floor system: The majority of manufactured homes are built with floor joists running either parallel or perpendicular to the length of the home and framed by perimeter joists. The floor assembly of each section of the home rests on the steel chassis, consisting of two steel I-beams. The design of most manufactured homes requires support for the chassis I-beams at several points, as well as at designated points along the marriage wall. Under HUD regulations, the chassis may not be removed from the manufactured home.
Foundations, including basements, must accommodate a home’s support requirements. Thus, basements for manufactured homes commonly feature heavy steel cross beams, for transferring the load to the basement walls, and columns in the center of the basement for marriage line support. Our engineers design these structural support elements.
Integrated floor system: An alternative design to the conventional chassis system is the integrated floor system. An integrated floor consolidates the floor joists and the chassis into a single structure. The home then has lower transportation and installation profiles, and is supported at the perimeter and centerline wall. This has obvious advantages for basement applications, as it typically eliminates the need for steel crossbeams and provides more flexibility in locating a stairwell to the basement.
METHODS OF ATTACHMENT
The basement design allows the entire perimeter length of the floor joist system to be attached to the top of the sill, the preferred and most economical approach – our engineers may suggest another method depending on your situation. The connection is secured with engineer-approved nailing strips (or approved steel nailing plates), fastened according to our engineer’s nailing schedule. The strips may then be painted and left as a finished surface.
Some states, such as Minnesota, have specific requirements for connections between the basement sill and a home’s floor to allow the soil pressures applied against the basement wall to be resisted by the floor diaphragm. If vinyl siding is to be applied over the sheathing, it is installed last.
CONSTRUCTION CHALLENGES
The basement is fully constructed before the home is installed. This presents a few challenges to the foundation contractor and home installer:
- The basement must be precisely measured and constructed. Installers/builders are advised to consult with the home manufacturer to obtain the exact floor dimensions and coordinate these dimensions with the engineered plans. There is less tolerance for error than if the foundation were intended for a site-built home, because such errors cannot be corrected by the floor framing carpenters, as they can when site building a home.
- The location and design of all under-floor utilities and structures (for example, drain lines, heat duct crossovers, steel chassis components, and axle hangers) must be considered in advance.
- The manufacturer must provide a “foundation ready” floor/chassis system, with steel chassis components sufficiently recessed to allow an 8-10 in. clearance from the edge of the floor joists. Alternatively, the manufacturer must construct the home on a floor/chassis system designed to allow a clear span between the basement wall and the marriage wall.
- Unless special precautions are taken, including coating the exterior of the walls with a water- tight sealant, basements are particularly susceptible to water penetration. We try design a water-tight sealant into all of our basement foundation plans.
- The home manufacturer must provide a stairwell design that permits entry to the basement.
COST
Basements are expensive compared to other types of foundation systems. However, basements can add significant amounts of usable space to a home.
REAL PROPERTY CLASSIFICATION
Properly designed basements would be expected to meet the conditions set for real property financing. Because the walls and connections are properly engineered by our team, basements effectively resist wind, gravity, and seismic forces.
INSTALLATION TIME
Constructing a basement requires more time than other foundation systems and, as indicated, is more complicated and requires a greater degree of precision. However, most of the site work is completed prior to the arrival of the home. Once the transporter delivers the home, the installation contractor positions the home over the basement either using the crane or roll-on methods described earlier. In either case, basement installations require more time than other systems
WIND LOAD RESISTANCE
With proper fastening of home to foundation, basements effectively resist wind loads. Due to the firm attachment techniques designed by our engineers and into every basement, the homes are well protected and secured to the ground.
GRAVITY LOAD RESISTANCE
In general, our basement designs offer good gravity load resistance. The weight of the home is transferred through the load-bearing walls or columns to the footers. In most cases, connections, even at the perimeter wall, are economically made.
SEISMIC LOAD RESISTANCE
Although earthquake risks are relatively low in most areas where basements are popular, the mass and depth of a basement, coupled with the attachment methods, offers good resistance against the effects of shaking from ground motion.
Ready to Order? If you are ready to order foundation plans, you may place your order by clicking here.
FLOOD RESISTANCE
Due to the fact that a basement can easily fill with water during a flood, this system is not recommended when building in a flood plain. In fact, the basement floor is considered the first floor of a residence under the FEMA National Flood Insurance Program. As such, it would fall below the base flood elevation level for such a home, and the home would not qualify for flood insurance.
FROST HEAVE
Full basements will have footings and concrete floors below any known frost line in the United States. Walkout basements, on the other hand, may need extra deep footings because the exit door threshold will be at grade level. Overall, basements are relatively impervious to frost-induced movement.