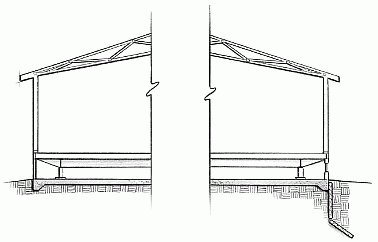
DESCRIPTION
A slab system designed by our engineers is a foundation that is considered to provide all necessary structural support to a manufactured home in an economical manner. The home is typically elevated above the slab, creating what appears to be a conventional crawl space under the home. However, to distinguish this group of foundations that, even in the coldest climates, sit above the frost line and are monolithic (i.e., the home sits on a single, integrated structural element), they are separately classified.
A slab is designed by our engineers that supports the home on top of the earth. The slab is uninsulated or insulated (same as a frost protected shallow foundation), depending on the local conditions and judgment of our engineers.
In this regard, the term “slab,” when applied to manufactured housing has a slightly different meaning than it does when used with stick-built homes. A slab used for a stick-built home is considered to be at once a structural support for the rest of the building (as it is for a manufactured home), and a semi-finished floor, over which linoleum, tile, wood, or carpeting is installed as the finished surface. All manufactured homes are delivered with full raised floors that include insulation and finished surfaces as well as electrical and plumbing systems and, in most areas, heating/cooling ducts. The slab under a manufactured home, therefore, does not act as the home’s floor, but rather as a platform for the home.
Slabs are not unique to manufactured homes. They are recognized and accepted for many other types of buildings, including site-built single-family homes and commercial structures. They are commonly found in areas with freezing and expansive soils.
Ready to Order? If you are ready to order foundation plans, you may place your order by clicking here.
Part of the reason slabs are economical is that they are relatively thin, extending only as deep as required to carry the structural loads. In northern climates with deep frost depths, the slab generally does not run to below the frost line. In such cases, the slab (often referred to as a “floating” slab) can shift as the soil underneath expands and contracts due to forces such as frost heave. This movement can be minimized or eliminated if the ground under the home is kept dry through the use of effective drainage techniques, such as drain tile and sump pumps. In contrast, properly designed crawl space and basement foundations remain fixed, even if the adjacent soil moves. The propensity of uninsulated slabs to shift with soil movement may keep them from meeting state or local requirements for a real property foundation and therefore from qualifying for real property financing.
An insulated slab (frost protected shallow foundation) is insulated around its perimeter, which keeps the ground under the slab warmer than the surrounding soil. For this design (commonly referred to as a shallow frost-protected foundation) to work during the coldest months, the crawl area ventilation must be closed to prevent cold outside air from cooling the space under the home and freezing the soil beneath the slab. The modest heat loss through the floor of the home keeps the crawl area warm and the insulation traps the heat in the soil, thus providing a heat sink that minimizes the chance of the ground freezing under the home. Although subject to review by the local authority, this design variation may qualify as a real property foundation.
The simple design of slabs minimizes the time required for fork work and
provides a level base for the home.
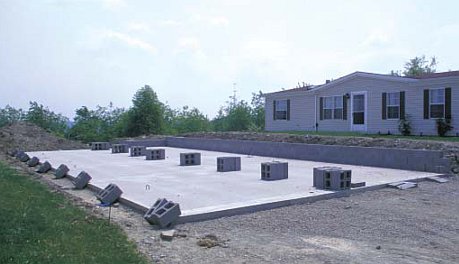
ADVANTAGES
The primary attraction of a slab is its relatively low cost. Due to the normal rectangular shape of the slab, the time and materials required for forming are minimal, compared to other concrete designs. Because there are no footings or piers extending down into the earth below the slab itself, in areas that have deep frost lines or expansive soils, the savings can be significant when compared to deep piers.
DISADVANTAGES
As noted earlier, uninsulated slabs are not typically used for homes intended to meet real property requirements. However, in areas where there is no frost or a relatively shallow frost line, the cost to qualify the foundation may be modest.
If the manufactured home will have an attached garage (which we can also engineer and create plans for), it may not be possible to economically pour a single slab for both structures, due to the vertical height difference between the garage slab and the floor of the house. The two foundations can be separated by an expansion joint, as any variation in movement between the home and the garage could be structurally damaging to either or both. Possible differential movement between adjacent slabs should be considered. A slab is less suitable than other designs for sloping lots. In most such instances, it is necessary to excavate to a level site (“cutting a level pad”).
CONSTRUCTION
A slab must be designed by our engineers to handle points of concentrated loads, such as centerline (ridge beam) piers, or distributed loads, such as along exterior walls. The slab must be able to resist upheaval pressure from the ground below and not fail to act as a structural unit or monolith.
A number of techniques and materials are used by our engineers to reinforce a slab. The variables that impact rigidity and durability include the overall thickness of the concrete and the incorporation of various types of reinforcing that are encased in concrete.
The use of post-tensioning, while not common for relatively lightweight construction applications like manufactured homes, is nevertheless a way to dramatically increase the strength and load-carrying capacity of concrete slabs.
SLAB VENTILATION
With rare exceptions, there is no difference between slab, anchor and pier, and crawl space foundations with respect to ventilation requirements. Adequate ventilation is needed to dissipate moisture migrating into the area under the home from other sources. Vents are normally provided in the exterior wall or the skirting surrounding the home. As with other foundations, provision for cross ventilation is essential. The area beneath a manufactured home installed on a slab is accessed through an opening in the exterior containment wall or skirting.
INSTALLATION
Generally, slabs offer a ready subsurface for the installation of a manufactured home. The home is merely driven over the slab for assembly. The hard and level slab provides an ideal working surface for the installers to complete the connection between foundation and home. Once rough-spotted, the close-off plastic can be stripped and the two (or more) sections leveled and mated together. The materials used for crawl space foundations can also be used for a slab. The most popular piering material is the hollow core concrete block. These blocks can be used at our engineered-specified points along the chassis I-beams and the mating wall, the latter for support of the ridge beam. Alternatively, a fabricated steel stanchion with screw thread cap can be used.
METHODS OF ATTACHMENT
To act in unison with its slab foundation, a home must be permanently anchored to the foundation. This is commonly accomplished through the use of anchors embedded in the concrete that our engineers analyze and design. Homes can also be permanently affixed through welded or bolted connections between the chassis and the piers, if the piers are themselves permanent. Examples of permanent piers are mortared and grouted concrete blocks, and steel stanchions bolted to the slab. The permanent attachment may also be through a structural, load-bearing exterior wall.
CONSTRUCTION CHALLENGES
Relative to basements and crawl space foundations, the slab offers fewer construction and installation challenges. Slabs are commonly poured somewhat wider and longer than the homes for which they are intended. Thus, less precision is required in their layout and preparation.
The uppermost challenge is the need to pour a high quality, well-reinforced singular mass of concrete, as it will literally become the ship upon which the house will sail in heaving soil conditions. There cannot be any chance of failure or breaking into disconnected sections, the consequences of which could be severe for the home.
A garage with a slab floor adjacent to the home’s floor need to be carefully designed by our engineers to offset pour and expansion joints between home and garage. Otherwise, any weak points in the concrete between the house and garage could grow to a large structural problem if the monolith separates under pressure and were to move independently of each other. This could create structural damage at the point where the house and garage connect.
COST
The overall cost of a typical slab, and the attendant material and labor to install a manufactured home upon it, falls in the low to mid-range of all foundations covered by this guide. More concrete is consumed than in simpler ribbon footing crawl space foundations. However, less form construction and less restrictive dimensional tolerances create savings. But the dramatic savings results from not having to excavate or pour concrete to any significant depth in the ground. Consequently, the relative cost savings increases in areas with deep frost lines.
REAL PROPERTY CLASSIFICATION
Except in the case of uninsulated slabs in areas with deep frost penetration, slab designs may be made to meet requirements for real property financing. In particular, insulated slabs and slabs used in areas with no frost penetration may meet the FHA real property criteria.
INSTALLATION TIME
A slab creates an ideal environment for the house installation process: The home’s footprint is over a firm, clean, and often dry platform. Level concrete is perfect for the safe and rapid lifting of a home with manual jacks to remove the wheels, axles, and hitches, and to rest the home upon its supports. These advantages usually speed up the installation process.
Ready to Order? If you are ready to order foundation plans, you may place your order by clicking here.
WIND LOAD RESISTANCE
A slab is an excellent base to which a house can be permanently secured with ground anchors embedded in concrete. After we engineer the anchorage and it is properly installed, these anchors can give a home the horizontal resistance necessary for wind load resistance. Because of varying wind load potential and standards across the country, our engineers design the anchorage device that is site specific for your exact home dimensions and geographic conditions.
GRAVITY LOAD RESISTANCE
Weight loads from the manufactured home and its future contents are designed by our engineers to be transferred to the ground and spread over a considerable area by the slab. This assures that the foundation can support the home even in the lower ranges of soil-bearing capacity.
SEISMIC LOAD RESISTANCE
In higher seismic zones, slabs are required to meet more stringent design and engineering requirements. A foundation system that is designed to move under pressure from the earth below is less suitable for use in the higher seismic risk zones. Seismic loads may be engineered by our staff that involve detailing connections for large withdrawal loads and the possibly designing the slab as a reinforced “structural mat” foundation.
FLOOD RESISTANCE
Although no home should ever be installed in a floodway, slabs can be used successfully to support homes located in the flood plain provided the floor of the home is above the 100-year base flood elevation. Knowledge of the soil upon which the slab is to be poured, with respect to its behavior when saturated, will help decide whether a slab is the best foundation selection in a flood plain. Standing water may act to scour the area under a shallow foundation, impairing its performance once floodwaters recede.
FROST HEAVE
After being designed by our engineers and correctly installed, slabs can resist the forces of frost heave. The two major strategies by our engineers: insulating the slab and taking steps to keep the ground under the slab dry (e.g., use of drain tiles) are proven and successful measures. Uninsulated slabs in frost-prone areas may be subject to shifting when exposed to frost conditions.